Liquid-Solid Fluidized Bed#
Features#
Solvers:
lethe-particles
andlethe-fluid-particles
Three-dimensional problem
Displays the selection of models and physical properties
Simulates a solid-liquid fluidized bed
Postprocessing code available
Files Used in This Example#
All files mentioned below are located in the example’s folder (examples/unresolved-cfd-dem/liquid-solid-fluidized-bed
).
Parameter file of particles generation and packing:
packing-particles.prm
Parameter file for CFD-DEM simulation of the liquid-solid fluidized bed:
liquid-solid-fluidized-bed.prm
Postprocessing Python script:
lsfb_postprocessing.py
Description of the Case#
This example simulates the fluidization of spherical particles in water. It is meant to reproduce the behavior observed experimentally in a pilot-scale equipment with the same characteristics as the simulations.
We use two different types of particles [1]: alginate \((d_p = 2.66 \: \text{mm}\), \(\rho_p = 1029 \: \text{kg} \cdot \text{m}^{-3})\) and alumina \((d_p = 3.09 \: \text{mm}\), \(\rho_p = 3586 \: \text{kg} \cdot \text{m}^{-3})\).
A representation of this equipment is shown. The fluidization region comprises a \(1.0 \: \text{m}\) height, \(10 \: \text{cm}\) diameter cylinder made of acrylic. More details about the experimental setup can be found in Ferreira et al. [1] and Ferreira et al [2].
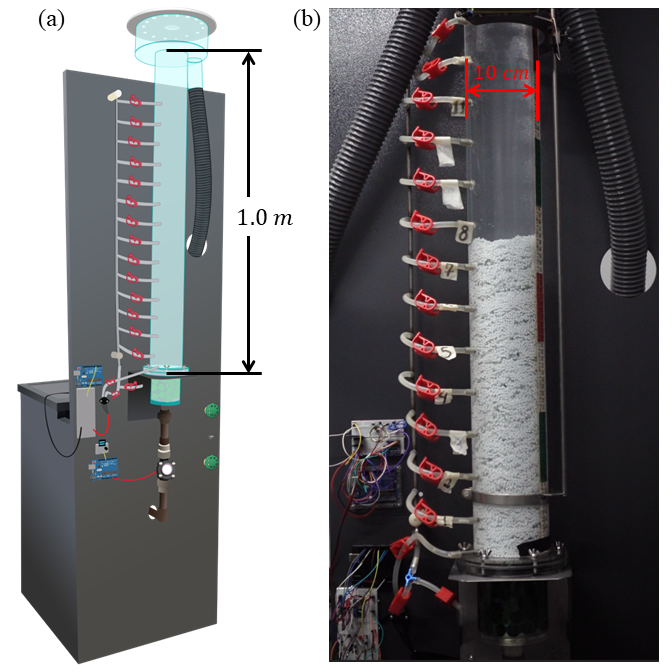
Pilot-scale fluidized bed used as reference for simulations in this example. Image includes (a) schematic representation of the bed and (b) picture of the equipment in operation. Adapted from Ferreira et al [1].#
DEM Parameter File#
As in the other examples of this documentation, we use Lethe-DEM to fill the bed with particles. We enable check-pointing in order to write the DEM checkpoint files which will be used as the starting point of the CFD-DEM simulation. Then, we use the lethe-fluid-particles
solver within Lethe to simulate the fluidization of the particles by initially reading the checkpoint files from the DEM simulation.
All parameter subsections are described in the Parameters section of the documentation.
To set-up the cylinder fluidized bed case, we first fill the bed with particles.
We first introduce the different sections of the parameter file packing-particles.prm
needed to run this simulation.
Mesh#
In this example, we are simulating a cylindrical fluidized bed that has a half length of \(0.55 \: \text{m}\) (\(10 \: \text{cm}\) higher than the fluidization region in the experimental setup), and a diameter of \(10 \: \text{cm}\). We use the subdivided_cylinder GridGenerator in order to generate the mesh. The cylindrical bed is divided \(132 \: \text{times}\) in the \(x\) direction (height) and \(12 \: \text{times}\) in \(y\) and \(z\) directions (\(6 \: \text{times}\) along the radius). The following portion of the DEM parameter file shows the function called:
subsection mesh
set type = dealii
set grid type = subdivided_cylinder
set grid arguments = 33:0.05:0.55
set initial refinement = 2
set expand particle-wall contact search = true
end
Note
Note that, since the mesh is cylindrical, set expand particle-wall contact search = true
. Details on this in the DEM mesh parameters guide.
A cross-section of the resulting mesh is presented in the following figure.
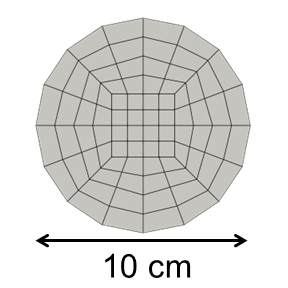
Cross-section of the mesh used in liquid-solid fluidized bed simulations.#
Floating Walls#
A floating wall is added \(10 \: \text{cm}\) above the bottom of the mesh, so that void fraction discontinuities can be avoided. The remaining region above the floating wall is \(1 \: \text{m}\) high, as in the experimental setup.
subsection floating walls
set number of floating walls = 1
subsection wall 0
subsection point on wall
set x = -0.45
set y = 0
set z = 0
end
subsection normal vector
set nx = 1
set ny = 0
set nz = 0
end
set start time = 0
set end time = 50
end
end
Note
Note that end time
is higher than time end
in simulation control
, so that the floating wall remains for the whole simulation.
Simulation Control#
Here, we define the time-step and the simulation end time.
subsection simulation control
set time step = 0.000005
set time end = 2.5
set log frequency = 20000
set output frequency = 20000
set output path = ./output_dem/
end
Important
It is important to define the time end
to include the time required to insert the particles and the time the it takes for particles to settle.
Restart#
The lethe-fluid-particles
solver requires reading several DEM files to start the simulation. For this, we have to write the DEM simulation information. This is done by enabling the check-pointing option in the restart subsection. We give the written files a prefix “dem” set in the set filename
option. The DEM parameter file is initialized exactly as the cylindrical packed bed example. The difference is in the number of particles, their physical properties, and the insertion box defined based on the new geometry. For more explanation about the individual subsections, refer to the DEM parameters and the CFD-DEM parameters.
subsection restart
set checkpoint = true
set frequency = 20000
set restart = false
set filename = dem
end
Model Parameters#
The subsection on model parameters is explained in the DEM model parameters guide and DEM examples.
subsection model parameters
subsection contact detection
set contact detection method = dynamic
set neighborhood threshold = 1.5
end
subsection load balancing
set load balance method = dynamic
set threshold = 0.5
set dynamic check frequency = 10000
end
set particle particle contact force method = hertz_mindlin_limit_overlap
set particle wall contact force method = nonlinear
set integration method = velocity_verlet
end
Lagrangian Physical Properties#
The lagrangian properties were taken from Ferreira et al [1].
subsection lagrangian physical properties
set g = -9.81, 0, 0
set number of particle types = 1
subsection particle type 0
set size distribution type = uniform
set diameter = 0.003087
set number = 72400
set density particles = 3585.9
set young modulus particles = 1e7
set poisson ratio particles = 0.3
set restitution coefficient particles = 0.9
set friction coefficient particles = 0.1
set rolling friction particles = 0.2
end
set young modulus wall = 1e7
set poisson ratio wall = 0.3
set restitution coefficient wall = 0.2
set friction coefficient wall = 0.1
set rolling friction wall = 0.3
end
The number of particles used for alginate particles is \(107\;\! 960\).
Insertion Info#
The volume of the insertion box should be large enough to fit all particles. Also, its bounds should be located within the mesh generated in the Mesh subsection.
subsection insertion info
set insertion method = volume
set inserted number of particles at each time step = 48841 # for alginate, we recommend 79600
set insertion frequency = 200000
set insertion box points coordinates = -0.15, -0.035, -0.035 : 0.53, 0.035, 0.035
set insertion distance threshold = 1.3
set insertion maximum offset = 0.3
set insertion prn seed = 19
end
Note
Particles need to be fully settled before the fluid injection. Hence, time end
in subsection simulation control
needs to be chosen accordingly.
Running the DEM Simulation#
Launching the simulation is as simple as specifying the executable name and the parameter file. Assuming that the lethe-particles
executable is within your path, the simulation can be launched in parallel as follows:
Lethe will generate a number of files. The most important one bears the extension .pvd
. It can be read by popular visualization programs such as Paraview.
Note
Running the packing of alumina particles should take approximately \(57 \: \text{minutes}\) on \(16 \: \text{cores}\). For the alginate particles, it takes approximately \(1 \: \text{hour}\) and \(53 \: \text{minutes}\).
Now that the particles have been packed inside the cylinder, it is possible to simulate the fluidization of particles.
CFD-DEM Parameter File#
The CFD simulation is to be carried out using the packed bed simulated in the previous step. We will discuss the different parameter file sections. The mesh section is identical to that of the DEM so it will not be shown again.
Simulation Control#
The long simulation is due to the small difference between particles and liquid densities, meaning that it takes very long to reach the pseudo-steady state.
subsection simulation control
set method = bdf1
set output name = cfd_dem
set output frequency = 100
set time end = 20
set time step = 0.001
set output path = ./output/
end
Since the alumina particles are more than \(3 \: \text{times}\) denser than alginate particles, the pseudo-steady state is reached after very different times (according to Ferreira et al [1]. \(4\) and \(10 \: \text{seconds}\) of real time, respectively). Because of this, we use set time end = 35
for the alginate.
Physical Properties#
The physical properties subsection allows us to determine the density and viscosity of the fluid. The values are meant to reproduce the characteristics of water at \(30 \: \text{°C}\).
subsection physical properties
subsection fluid 0
set kinematic viscosity = 0.0000008379
set density = 997
end
end
Initial Conditions#
For the initial conditions, we choose zero initial conditions for the velocity.
subsection initial conditions
set type = nodal
subsection uvwp
set Function expression = 0; 0; 0; 0
end
end
Boundary Conditions#
For the boundary conditions, we choose a slip boundary condition on the walls (id = 0
) and an inlet velocity of \(0.157\;\! 033 \: \text{m/s}\) at the lower face of the bed (id = 1
).
subsection boundary conditions
set number = 2
subsection bc 0
set id = 0
set type = slip
end
subsection bc 1
set id = 1
set type = function
subsection u
set Function expression = 0.157033
end
subsection v
set Function expression = 0
end
subsection w
set Function expression = 0
end
end
end
The following sections for the CFD-DEM simulations are the void fraction subsection and the CFD-DEM subsection. These subsections are described in detail in the CFD-DEM parameters .
Void Fraction#
We choose the particle centroid method (PCM) to calculate void fraction. The l2 smoothing length
we choose is around twice the particle’s diameter, as in the other examples.
subsection void fraction
set mode = pcm
set read dem = true
set dem file name = dem
set l2 smoothing length = 0.005328
end
CFD-DEM#
Different from gas-solid fluidized beds, buoyancy, pressure force, shear stress are not negligible. All these forces are considered in this example.
Saffman lift force is proven to be very important to properly reproduce particles’ dynamics in the liquid-fluidized bed [1].
subsection cfd-dem
set vans model = modelA
set grad div = true
set drag model = rong
set buoyancy force = true
set shear force = true
set pressure force = true
set saffman lift force = true
set coupling frequency = 100
set void fraction time derivative = false
end
Warning
Void-fraction time-derivative lead to significant instability in the case of liquid-fluidized beds, hence we do not use it.
Non-linear Solver#
We use the inexact Newton non-linear solver to minimize the number of time the matrix of the system is assembled. This is used to increase the speed of the simulation, since the matrix assembly requires significant computations.
subsection non-linear solver
subsection fluid dynamics
set solver = inexact_newton
set tolerance = 1e-10
set max iterations = 10
set verbosity = verbose
end
end
Linear Solver#
subsection linear solver
subsection fluid dynamics
set method = gmres
set max iters = 5000
set relative residual = 1e-3
set minimum residual = 1e-11
set preconditioner = ilu
set ilu preconditioner fill = 1
set ilu preconditioner absolute tolerance = 1e-14
set ilu preconditioner relative tolerance = 1.00
set verbosity = verbose
end
end
Running the CFD-DEM Simulation#
The simulation is run (on \(8 \: \text{cores}\)) using the lethe-fluid-particles
application as follows:
The \(20\)-second simulations with alumina took approximately \(24 \: \text{hours}\) and \(30 \: \text{minutes}\) on \(16 \: \text{cores}\) and \(8 \: \text{hours}\) and \(44 \: \text{minutes}\) on \(32 \: \text{cores}\).
The \(35\)-second simulations with alginate particles took about \(28 \: \text{hours}\) on \(16 \: \text{cores}\).
Results#
We briefly comment on some results that can be extracted from this example.
Important
This example includes a postprocessing file written in Python that uses the lethe_pyvista_tools. module.
Important
To use the code, run python3 lsfb_postprocessing.py $PATH_TO_YOUR_CASE_FOLDER
. The code will generate several graphics showing the pressure profile within the bed, which are going to be stored in $PATH_TO_YOUR_CASE_FOLDER/P_x
. It will also generate a deltaP_t.csv
file with the total pressure difference for each time-step. Additionally, it generates a void fraction as a function of time graphic (eps_t.png
).
Important
You need to ensure that the lethe_pyvista_tools
is working on your machine. Click here for details.
Side View#
Here we show comparison between the experimentally observed and simulated behavior of the liquid-solid fluidized bed with alumina.
The void fraction and velocity profile of the fluid are also shown.
Total Pressure Drop and Bed Expansion#
In fluidized beds, the total pressure drop (\(- \Delta p\)) reflects the total weight of particles (\(M\)). The following equation is derived from a force balance inside the fluidized bed [3].
where \(H\) is the total bed height, \(\bar{\varepsilon}_f\) is the average fluid fraction (void fraction) at the bed region, \(\rho_p\) and \(\rho_f\) are the densities of the particles and the fluid (respectively), and \(A\) is the cross-section area of the equipment.
Liquid fluidized beds are very uniform in terms of particles distribution, resulting in an uniform distribution of \(\varepsilon_f\) along the be height. From this hypothesis, we can conclude that, for a constant and uniform fluid inlet flow rate, the pressure slope is:
With the pressure slope, it is also possible to determine the bed void fraction manipulating the first equation, which gives:
The resulting behavior of the pressure along the bed height and the void fraction with time is shown in the following animation.
Particles Dynamics#
Since the fluidization occurs in a high density fluid, the density difference between alginate and alumina particles have a significant impact on the velocity of the particles inside the bed.
The following animation is in real time. It is possible to notice that, for a similar bed height, the bed of alumina particles expands way faster than the alginate.