Boycott Effect#
Features#
Solvers:
lethe-particles
andlethe-fluid-particles
Three-dimensional problem
Displays the selection of models and physical properties
Simulates a solid-liquid sedimentation
Files Used in This Example#
Both files mentioned below are located in the example’s folder (examples/unresolved-cfd-dem/boycott-effect
).
Parameter file for initial particles generation:
initial-particles.prm
Parameter file for CFD-DEM simulation of the Boycott effect:
boycott-effect.prm
Description of the Case#
This example simulates the sedimentation of a group of particles in a viscous fluid. Two cases were simulated. In the first case, the channel is placed vertically. In the second case, the channel is inclined at \(20^{\circ}\) with respect to the gravity. First, we use lethe-particles
to insert the particles. We enable check-pointing in order to write the DEM checkpoint files which will be used as the starting point of the CFD-DEM simulation. Then, we use the lethe-fluid-particles
solver within Lethe to simulate the sedimentation of particles by initially reading the checkpoint files from the DEM simulation.
DEM Parameter File#
We introduce the different sections of the parameter file boycott-effect.prm
needed to run this simulation. Most subsections are explained in detail in other CFD-DEM examples such as: Gas-solid spouted bed. Therefore, we will not go over them in detail.
Mesh#
In this example, we are simulating a rectangular channel. We use the deal.II GridGenerator in order to generate a hyper rectangle that is subdivided along its height. The following portion of the DEM parameter file shows the function called:
subsection mesh
set type = dealii
set grid type = subdivided_hyper_rectangle
set grid arguments = 15,70,15:-0.03,0,-0.03:0.03,0.4,0.03:true
set initial refinement = 0
set expand particle-wall contact search = false
end
Simulation Control#
The time step in this case is the same as the time end. Since we only seek to insert the particles at the top of the channel, we only require 1 insertion time step. We do not need the particles to be packed, therefore by doing this, the particles will be inserted, but will not fall under the action of gravity.
subsection simulation control
set time step = 1e-6
set time end = 1e-6
set log frequency = 1000
set output frequency = 1
set output path = ./output_dem/
end
Restart#
We save the files obtained from the single iteration by setting the frequency = 1. These files will be used to start the CFD-DEM simulation.
subsection restart
set checkpoint = true
set frequency = 1
set restart = false
set filename = dem
end
Model Parameters#
The section on model parameters is explained in the DEM examples. We show the chosen parameters for this section:
subsection model parameters
subsection contact detection
set contact detection method = dynamic
set neighborhood threshold = 1.3
set frequency = 1
end
set rolling resistance torque method = constant_resistance
set particle particle contact force method = hertz_mindlin_limit_force
set particle wall contact force method = nonlinear
set integration method = velocity_verlet
end
Lagrangian Physical Properties#
The gravity is set to 0 as we only need to insert the particles in the specified insertion box.
subsection lagrangian physical properties
set g = 0.0, 0.0, 0.0
set number of particle types = 1
subsection particle type 0
set size distribution type = uniform
set diameter = 0.002
set number = 8379
set density particles = 1200
set young modulus particles = 1e6
set poisson ratio particles = 0.25
set restitution coefficient particles = 0.97
set friction coefficient particles = 0.3
set rolling friction particles = 0.1
end
set young modulus wall = 1e6
set poisson ratio wall = 0.25
set restitution coefficient wall = 0.97
set friction coefficient wall = 0.3
set rolling friction wall = 0.1
end
Insertion Info#
We insert the particles uniformly in the specified insertion box at the top of the channel.
subsection insertion info
set insertion method = volume
set inserted number of particles at each time step = 8379
set insertion frequency = 2000
set insertion box points coordinates = -0.025, 0.3, -0.025 : 0.026, 0.396, 0.026
set insertion distance threshold = 1.2
set insertion maximum offset = 0.
set insertion prn seed = 19
end
Running the DEM Simulation#
Launching the simulation is as simple as specifying the executable name and the parameter file. Assuming that the lethe-particles
executable is within your path, the simulation can be launched on a single processor by typing:
or in parallel (where 8 represents the number of processors)
The figure below shows the particles inserted at the top of the channel at the end of the DEM simulation.
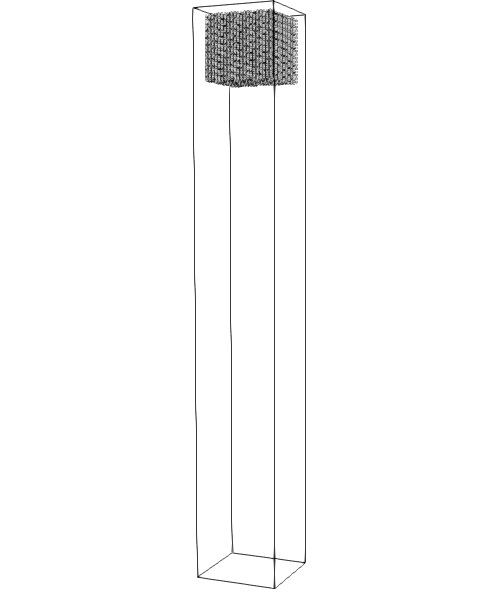
After the particles have been inserted it is now possible to simulate the sedimentation of particles.
CFD-DEM Parameter File#
The CFD simulation is to be carried out using the particles inserted within the previous step. We will discuss the different parameter file sections. Some sections are identical to that of the DEM so they will not be shown again.
Simulation Control#
The simulation is run for \(2\) s with a time step of \(0.005\) s. The time scheme chosen for the simulation is first order backward difference method (BDF1). The simulation control section is shown:
subsection simulation control
set method = bdf1
set number mesh adapt = 0
set output name = result_
set output frequency = 20
set time end = 2
set time step = 0.005
set output path = ./output/
end
Physical Properties#
The physical properties subsection allows us to determine the density and viscosity of the fluid. We choose a density of \(1115.6\) and a kinematic viscosity of \(0.00000177\) as to simulate the flow of a sugar-water solution with \(20\) % by weight sugar at \(20^{\circ}\) C. The dynamic viscosity of a 20 % sugar-water solution by weight at \(20^{\circ} C\) is 1.97 cP.
subsection physical properties
subsection fluid 0
set kinematic viscosity = 0.00000177
set density = 1115.6
end
end
Initial Conditions#
For the initial conditions, we choose zero initial conditions for the velocity.
subsection initial conditions
set type = nodal
subsection uvwp
set Function expression = 0; 0; 0; 0
end
end
Boundary Conditions#
For the boundary conditions, we choose a slip boundary condition on all the walls of the channel and the channel except the bottom and the top of the channel where a no-slip boundary condition is imposed. For more information about the boundary conditions, please refer to the Boundary Conditions Section
subsection boundary conditions
set number = 6
subsection bc 0
set id = 0
set type = slip
end
subsection bc 1
set id = 1
set type = slip
end
subsection bc 2
set id = 2
set type = noslip
end
subsection bc 3
set id = 3
set type = noslip
end
subsection bc 4
set id = 4
set type = slip
end
subsection bc 5
set id = 5
set type = slip
end
end
Lagrangian Physical Properties#
This section is identical to the one previously mentioned for the DEM simulation of particle insertion. The only difference is the definition of gravity. For the vertical case, we set \(g_y = -9.81\) and \(g_x = g_z = 0\). For the inclined case, we determine the gravity by setting: \(g_x = \frac{-9.81}{cos \theta}, \; g_y = \frac{-9.81}{sin \theta}, \; g_z = 0\) where \(\theta\) is the angle of inclination with the vertical.
The additional sections for the CFD-DEM simulations are the void fraction subsection and the CFD-DEM subsection. These subsections are descrichannel in detail in the CFD-DEM parameters .
Void Fraction#
Since we are calculating the void fraction using the particle insertion of the DEM simulation, we set the mode
to dem
. For this, we need to read the dem files which we already wrote using check-pointing. We, therefore, set the read dem
to true
and specify the prefix of the dem files to be dem.
We choose to use the quadrature centered method (QCM) to calculate the void fraction. For this, we specify the mode
to be qcm
. We want the radius of our volume averaging sphere to be equal to the length of the element where the void fraction is being calculated. We don’t want the volume of the sphere to be equal to the volume of the element.
For this, we set the qcm sphere equal cell volume
equals to false
. Unlike the other schemes, we do not smooth the void fraction as we usually do using the PCM and SPM void fraction schemes since QCM is continuous in time and space.
subsection void fraction
set mode = qcm
set qcm sphere equal cell volume = false
set read dem = true
set dem file name = dem
end
CFD-DEM#
We also enable grad-div stabilization in order to improve local mass conservation. If we were using PCM and SPM void fraction schemes, the void fraction time derivative should be disabled as the time variation of the void fraction will lead to unstable simulations. The source of such instability is the first term of the continuity equation \(\rho_f \frac{\partial \varepsilon_f}{\partial t}\), which is stiff and unstable for the slightest temporal discontinuity of the void fraction and as \(\Delta t \to 0\). However, as we are using the QCM void fraction scheme, this term can be enabled. Usually, this term is neglected, however; disabling this term affects the results as we are no longer solving for the actual Volume Averaged Navier-Stokes equations. Therefore, we should not neglect this term based on numerical reasoning without any physical explanation.
subsection cfd-dem
set grad div = true
set void fraction time derivative = true
set drag force = true
set buoyancy force = true
set shear force = true
set pressure force = true
set drag model = difelice
set coupling frequency = 250
set grad-div length scale = 0.005
set vans model = modelA
end
We determine the drag model to be used for the calculation of particle-fluid forces. We enable buoyancy, drag, shear and pressure forces. For drag, we use the Di Felice model to determine the momentum transfer exchange coefficient. The VANS model we are solving is model A. Other possible option is model B.
Finally, the linear and non-linear solver controls are defined.
Non-linear Solver#
subsection non-linear solver
subsection fluid dynamics
set solver = inexact_newton
set tolerance = 1e-8
set max iterations = 10
set verbosity = verbose
set matrix tolerance = 0.75
end
end
We use the inexact_newton
solver as to avoid the reconstruction of the system matrix at each Newton iteration. For more information about the non-linear solver, please refer to the Non Linear Solver Section
Linear Solver#
subsection linear solver
subsection fluid dynamics
set method = gmres
set max iters = 5000
set relative residual = 1e-3
set minimum residual = 1e-10
set preconditioner = ilu
set ilu preconditioner fill = 0
set ilu preconditioner absolute tolerance = 1e-12
set ilu preconditioner relative tolerance = 1
set verbosity = verbose
set max krylov vectors = 200
end
end
For more information about the linear solver, please refer to the Linear Solver Section
Running the CFD-DEM Simulation#
The simulation is run using the lethe-fluid-particles
application. Assuming that the executable is within your path, the simulation can be launched as per the following command:
Results#
The results are shown in an animation below. The sedimentation of the particles in a vertical and inclined channel demonstrate different behaviors. This clearly shows the boycott effect as the fluid circulates in the inclined channel resulting in a larger velocity for both the fluid and particles. Thus, the particles fall further compared to the vertical channel where the fluid velocity is almost null, and the particles’ acceleration is low.