Sedimentation of One Particle#
This example aims to numerically reproduce the results obtained by Ten Cate et al. [1] for the E4 experience. This experience measures the velocity of the sedimentation of a 1.5 cm particle in a container filled with a viscous fluid. The container is sufficiently small to impact the particle sedimentation.
Warning
This case is a computationally expensive example. It can take several hours to run on a desktop computer.
Features#
Solvers:
lethe-fluid-sharp
(with Q1-Q1)Transient problem
Displays the capability of the resolved CFD-DEM solver for the flow around one particle
Files Used in This Example#
Parameter file:
/examples/sharp-immersed-boundary/sedimentation-1-particle/sedimentation-1-particle.prm
Description of the Case#
The E4 experiment consists of the release of a particle made of Nylon (\(\rho_p=0.001120 \frac{\text{kg}}{\text{cm}^{3}}\)) with a diameter of 1.5cm. The center of the particle is located 12.75 cm above the bottom of a 10x16x10 cm container. The viscosity of the fluid is \(\mu_f=0.00058 \frac{\text{kg}}{\text{s cm}}\) which is equivalent to \(\mu_f=0.058 \frac{\text{N s}}{\text{m}^{2}}\). The density of the fluid is \(\rho_f=0.000960 \frac{\text{kg}}{\text{cm}^{3}}\). The gravity constant is \(g= -981 \frac{\text{cm}}{\text{s}^{2}}\). The particle accelerates due to gravity until it hits the bottom of the container, at which point we stop the simulation.
Note
You will note that we have transformed every length unit into centimeters. The reason is that the particle’s size is very close to 1 cm. Representing the problem in this way helps the linear solver converge. It avoids extremely small values in the matrix due to the volume of cells being expressed in \(\text{cm}^{3}\) instead of \(\text{m}^{3}\).
All the container walls have no-slip boundary conditions except at the top of the container, where we define an open boundary.
Parameter File#
We explain every part of this parameter file in detail. In each section of the parameter file, we describe relevant parameters. The omitted parameters are only user preference parameters and do not impact the simulation results. For more detail, we suggest visiting the Parameters Guide.
Simulation Control#
subsection simulation control
set method = bdf2
set bdf startup method = multiple step bdf
set time step = 0.0025 # Time step
set time end = 1.3 # End time of simulation
set output name = out # Prefix for VTU outputs
set output frequency = 1 # Frequency of simulation output
end
The
method
is set tobdf2
to have a second-order time-stepping method. This ensures a low error due to the time discretization in this case.The
bdf startup method
is set tomultiple step bdf
as we do not have an initial solution that allows us to generate previous time steps. We use a multiple step bdf approach that will ramp the order of the scheme in the first few time steps.The
time step
is set to 0.0025. This ensures a low error due to the time discretization for this case.The
time end
is set to 1.3. This is slightly longer than the experimental results of Ten Cate et al. [1]. This ensures that the entire trajectory of the particle has been simulated.
Physical Properties#
subsection physical properties
subsection fluid 0
set kinematic viscosity = 0.6041666666666
set density = 0.000960
end
end
The
kinematic viscosity
is set to 0.6041666666666. This value is derived from the case description by dividing \(\mu_f\) by \(\rho_f\).
FEM#
subsection FEM
set velocity order = 1
set pressure order = 1
end
Here we use Q1-Q1 elements. This case is only for demonstration purposes as such we want to propose a simulation that is not too costly to run.
Mesh#
subsection mesh
set type = dealii
set grid type = subdivided_hyper_rectangle
set grid arguments = 5,8,5: 0,0,0 : 10 , 16 ,10 : true
set initial refinement = 1
end
The domain is a rectangular box as such we can directly use a subdivided hyper rectangle mesh from the deal.II library. In this case, we have orientated the y-direction with gravity. As such, we have the long side of the box along this axis.
The
grid arguments
is set to5,8,5: 0,0,0 : 10 , 16 ,10 : true
. This section has 3 subsections. First5,8,5
describes the initial subdivision of the box. This subdivision has been chosen as it is the smallest mesh we can do of the box in order to have cubic elements. Secondly0,0,0 : 10 , 16 ,10
describes the 2 points from which we have derived the rectangular box (0,0,0) and (10,16,10). Finally, we havetrue
, which is a boolean to activate the coloration of the boundary. This allows us to define separate boundary conditions at each side of the box.The
initial refinement
is set to 1. This will ensure to have a base mesh that is a bit smaller than the particle.
Mesh Adaptation#
subsection mesh adaptation
# Fraction of coarsened elements
set fraction coarsening = 0.3
# Fraction of refined elements
set fraction refinement = 0.05
# How the fraction of refinement/coarsening are interepreted. Choices are
# <number|fraction>.
set fraction type = number
# Frequency of the mesh refinement
set frequency = 1
# Maximum number of elements
set max number elements = 750000
# Maximum refinement level
set max refinement level = 6
# minimum refinement level
set min refinement level = 0
# Type of mesh adaptationChoices are <none|uniform|kelly>.
set type = kelly
# Variable for kelly estimationChoices are <velocity|pressure>.
set variable = velocity
end
The
fraction coarsening
is set to 0.3. This limits the accumulation of elements when the particle is moving. It allows for cells far from the particle to be coarsened when the particles get further away.The
fraction refinement
is set to 0.05. The objective here is to refine elements that become close to the particle when it’s moving. This will mostly refine elements around the particle that are not included in the refinement zone around the particle. The refinement zone around the particle will be discussed in more detail in the IB particle section.The
set frequency
is set to 1. Since the particle is moving at each time step, the refinement zone around it should be reevaluated at each time step.The
max refinement level
is set to 6. This parameter limits how small the elements around the particle can get limiting the total number of elements in the problem. Here we limit the mesh size to 48 elements per diameter of the particle. This should be sufficient to get accurate results.The
type
is set tokelly
. Since the particle is moving and we do not want a uniform refinement of all the cells, we use the kelly error estimator based on thevelocity
variable.
Boundary Conditions#
subsection boundary conditions
set number = 6
subsection bc 0
set id = 0
set type = noslip
end
subsection bc 1
set id = 1
set type = noslip
end
subsection bc 2
set id = 2
set type = noslip
end
subsection bc 3
set id = 3
set type = outlet
set beta = 0
end
subsection bc 4
set id = 4
set type = noslip
end
subsection bc 5
set id = 5
set type = noslip
end
end
Here we define the 5 no slip
boundary for all the box walls and specify the boundary with id=3
to an outlet representing the top of the box. We refer the reader to the Boundary Conditions - CFD section on how those boundaries are defined.
Note
The boundary id of dealii rectangular mesh are numbered as such: \(x_{min}=0\), \(x_{max}=1\), \(y_{min}=2\), \(y_{max}=3\), \(z_{min}=4\), \(z_{max}=5\).
Initial Conditions#
subsection initial conditions
# Type of initial conditionChoices are <L2projection|viscous|nodal>.
set type = nodal
subsection uvwp
set Function expression = 0; 0; 0;0
end
end
The initial condition for this case is simple to define. At the start of the simulation, we assume that the particle and the fluid are at rest. From there, we define a uniform velocity field of 0 everywhere. To do that, we used the type = nodal
and then specified a function expression of 0 for all the velocity components.
Non-linear Solver#
subsection non-linear solver
subsection fluid dynamics
set verbosity = verbose
set tolerance = 1e-6
set max iterations = 10
set residual precision = 5
set force rhs calculation = true
end
end
The
tolerance
is set to 1e-6. This is small enough to ensure that the flow field is adequately resolved, as here, we expect a velocity of the particle of the order of 10.The
max iterations
is set to 10. The objective here is to allow enough Newton non-linear steps to ensure the convergence to the tolerance. Also, we should limit the time pass on a single time step if the system is too stiff.- The
force rhs calculation
is set totrue
. This is the most important modification with most of the other examples. By default, the non-linear solver will recalculate the RHS only after the update of the solution. But here, we need to evaluate it before every matrix resolution, and we cannot use the last RHS evaluation that was done after the last newton iteration. The particle position was updated between these two steps, changing the RHS evaluation. This means that for every non-linear step, we evaluate the RHS twice. The non-linear solver follows this sequence of steps for each newton iteration. update the particle position
update the Jacobian matrix
update the RHS
solve the matrix system
reevaluate the RHS to check the convergence.
- The
Linear Solver#
subsection linear solver
subsection fluid dynamics
set method = gmres
set max iters = 1000
set relative residual = 1e-4
set minimum residual = 1e-11
set preconditioner = ilu
set ilu preconditioner fill = 0
set ilu preconditioner absolute tolerance = 1e-20
set ilu preconditioner relative tolerance = 1.00
set verbosity = verbose
set max krylov vectors = 1000
end
end
The
method
is set togmres
. This solver is less computationally expensive than the other option, and this case does not require any special preconditioner. This makes thegmres
solver withilu
preconditioner the best option available.The
max iters
is set to 1000. This is a lot more steps than how much it should take to solve the system.The
max krylov vectors
is set to the same number as the maximum solver iterations. This is to ensure that we keep the full Arnoldi basis for each new iteration. From experience keeping a maximum of Krylov vector results in a faster resolution for this case than clearing the basis after a certain number ofgmres
iterations.The
relative residual
is set to 1e-4. This is small enough, so we don’t under-resolve our matrix and do extra non-linear steps because of it, and at the same, it doesn’t require too manygmres
iterations.The
ilu preconditioner fill
is set to 0. This is the cheapest option. In this case, we can use this option without having to do too manygmres
iterations. It requires less computational time to do a few moregmres
iterations than building the preconditioner and doing fewergmres
iterations.
IB Particles#
subsection particles
set assemble Navier-Stokes inside particles = false
set number of particles = 1
subsection extrapolation function
set length ratio = 2
set stencil order = 3
end
subsection local mesh refinement
set initial refinement = 6
set refine mesh inside radius factor = 0.8
set refine mesh outside radius factor = 1.3
end
subsection DEM
set particle nonlinear tolerance = 1e-5
subsection gravity
set Function expression = 0;-981;0
end
end
subsection particle info 0
set type = sphere
set shape arguments = 0.75
set integrate motion = true
subsection position
set Function expression = 5;12.75;5
end
subsection velocity
set Function expression = 0;0;0
end
subsection physical properties
set density = 0.001120
end
end
end
In this subsection, we define most of the parameters that are related to the particle.
The
number of particles
is set to one as we only want one particle.stencil order
is set to 3 as this is the highest order we can use for this case, and it will not lead to Runge instability.refine mesh inside radius factor
is set to 0.8. This creates a mesh refinement around the particle that avoids having hanging nodes in the calculation and helps ensure a small enough mesh around the particle.refine mesh outside radius factor
is set to 1.3. This creates a mesh refinement around the particle that avoids having hanging nodes in the calculation and helps ensure a small enough mesh around the particle.initial refinement
is set to 6. Here we want to have the mesh as small as possible for the first time step. To achieve this, we refine every element with at least one vertex in the refinement zone around the particle 6 times before the simulation starts. This ensures that all the cells in the refinement zone around the particle is as small as possible. This number of refinements is 1 more than necessary. This is to avoid having part of the particle not properly refined as the initial mesh is big enough that some elements cut by the IB may not be properly detected at the beginning of the process. Doing one more refinement ensures that all the elements are properly refined.integrate motion
is set to true because we are interested in the dynamic of the particle as it sediments in the rectangular box.assemble Navier-Stokes inside particles
is set to false because we are not interested in the flow inside of the particle.length ratio
has been set to 2. This is small enough, so it does not impact too much the conditioning of the matrix while avoiding interpolation of the immersed boundary stencil in multiple elements.particle nonlinear tolerance
has been set to 1e-5. This is small enough to ensure that the particle dynamics are adequately resolved. We expect a velocity of the particle of the order of 10.gravity
Function expression
is set to 0;-981;0 according to the definition of the case. As we choose the long axis of the rectangular box along the Y, we define gravity in this direction.
The following parameters are defined in the particle subsection.
position
Function expression is set to 5;12.75;5. This is the initial position of the particle according to the description of the case.velocity
Function expression is set to 0;0;0. This is the initial velocity of the particle since it starts at rest.radius
is set to 0.75. This is according to the definition of the case where the particle has a diameter of 1.5 cm.density
is set to 0.001120. This is according to the definition of the case.
Running the Simulation#
Call lethe-fluid-sharp
by invoking the following command:
to run the simulation using fourteen CPU cores. Feel free to use more CPU cores.
Warning
Make sure to compile Lethe in Release mode and run in parallel using mpirun. This simulation takes \(\sim \, 4\) hours on \(14\) processes.
Results#
In this section, we will briefly show some results of this simulation.
First, we look at a slice of the velocity profile during the acceleration phase.
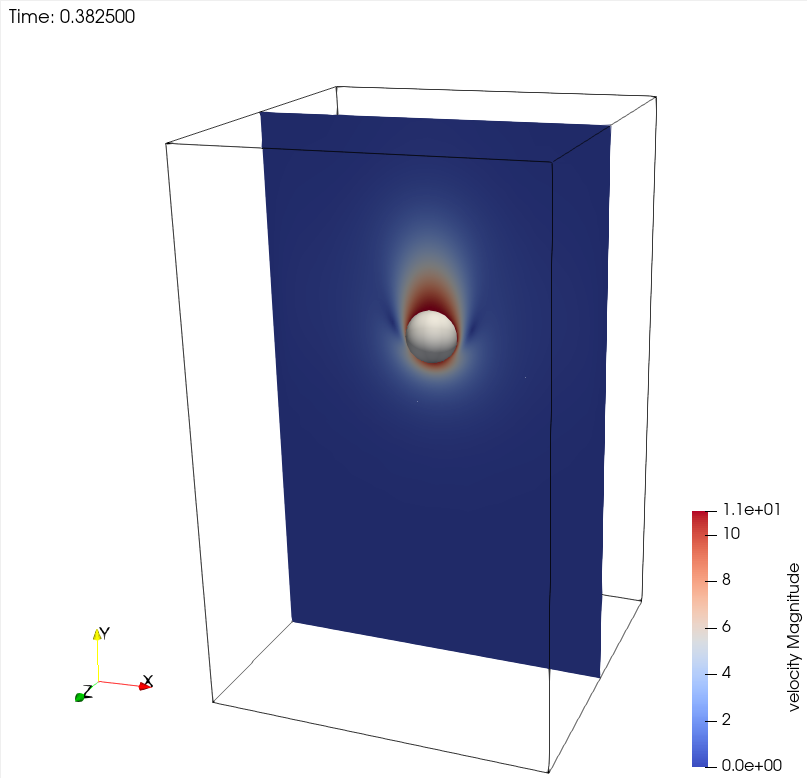
We can also compare the results obtained for the velocity in time with the results proposed by the article of Ten Cate et al. [1]
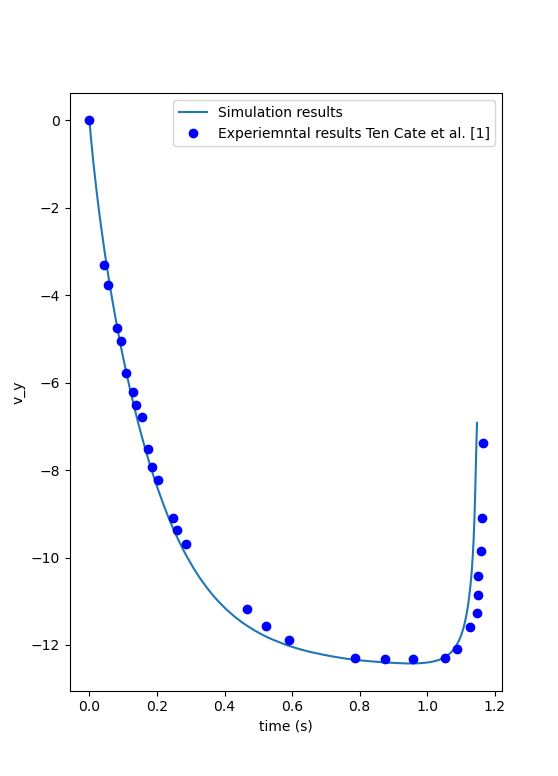