Turbulent Taylor-Couette Flow#
This example showcases a turbulent extension of the Taylor-Couette Flow. It features the matrix-free solver (lethe-fluid-matrix-free
) which is more computationally efficient when solving problems using high-order elements and fine meshes. It also demonstrates the utilization of initial conditions and the postprocessing of the enstrophy.
Features#
Solvers:
lethe-fluid-matrix-free
(with Q2-Q2 or Q3-Q3)Transient problem using
bdf2
time integratorDemonstrates the implementation of initial conditions for velocity and pressure
Demonstrates the postprocessing of the enstrophy
Files Used in This Example#
All files mentioned below are located in the example’s folder (examples/incompressible-flow/3d-turbulent-taylor-couette
).
Parameter file:
tc-matrix-free.prm
Reference data files from Wang and Jourdan (2021): [1] (
enstrophy_wang_p%.dat
)Postprocessing Python scripts:
tc-postprocessing.py
andtc-functions.py
Description of the Case#
The Taylor-Couette flow occurs in the annular space between two coaxial cylinders with different angular velocities. For a laminar flow, an analytical solution exists (see Taylor-Couette Flow). As the Reynolds number increases, the flow undergoes a transition where Taylor vortices emerge (symmetrical vortices in the radial-vertical plane). Eventually, as the flow becomes fully turbulent, a chaotic vortex structure appears with intense fluid agitation [2] .
This example is drawn from a case study by Wang and Jourdan [1]. It simulates a turbulent Taylor-Couette flow with a Reynolds number of 4000. It incorporates initial conditions based on a modified version of the laminar solution to generate specific vortical structures, inspired by the Taylor-Green vortex.
The inner cylinder rotates counterclockwise at a constant angular velocity \(\omega\), while the outer cylinder remains fixed. Periodic boundary conditions are applied to the upper and lower openings of the annular section. The following figure illustrates the geometry of this case:
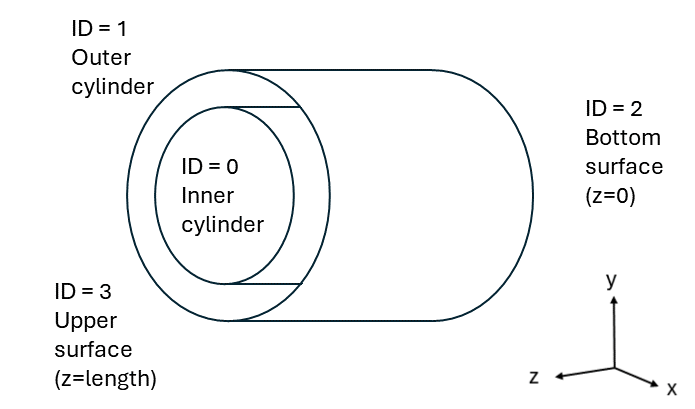
The initial conditions for velocity and pressure are defined as follows:
where \(A = -\frac{\omega \kappa^2}{1-\kappa^2}\), \(B = \frac{\omega r_i^2}{1-\kappa^2}\), \(U = \omega r_i\), \(\kappa = \frac{r_i}{r_o}\), \(d = r_o - r_i\), \(\epsilon\) is a relaxing factor, \(r_i\) is the inner cylinder radius, \(r_o\) is the outer cylinder radius, r is the radial coordinate and z is the axial coordinate.
For this particular case, the value for each variable can be found in the following table:
Variable |
Value |
Variable |
Value |
---|---|---|---|
A |
-0.3333 |
B |
0.3333 |
U |
0.5 |
\(\kappa\) |
0.5 |
d |
0.5 |
\(\epsilon\) |
0.1 |
\(r_i\) |
0.5 |
\(r_o\) |
1.0 |
Since Lethe uses a Cartesian coordinate system, the expressions have been transformed to proceed with the simulation. For an incompressible flow, the enstrophy and the kinetic energy are defined as:
where \(\mathbf{\omega}=\nabla \times \mathbf{u}\) represents the vorticity. The results obtained for both enstrophy and kinetic energy are compared to the benchmark values from the case study.
Parameter File#
Mesh#
The mesh
subsection specifies the computational grid:
subsection mesh
set type = dealii
set grid type = cylinder_shell
set grid arguments = 3.14159265359 : 0.5 : 1.0 : 5 : 4 : true
set initial refinement = 4
set initial boundary refinement = 1
set boundaries refined = 0, 1
end
The type
specifies the mesh format used. We use the cylinder_shell
from deal.II GridGenerator that creates a shell from two concentric cylinders with the option to set-up specific boundary conditions to each surface. The arguments are the length (3.14159265359), the inner cylinder radius (0.5), the outer cylinder radius (1.0), the number of azimuthal cells (5) and the number of axial cells (4).
Indicating an initial refinement = 4
implies that the initial mesh is refined 4 times globally; in 3D each cell is divided by 8 per refinement. However, in addition to this global refinements, the cells next to the walls are refined one more time locally. This is indicated through the initial boundary refinement = 1
parameter and the set boundaries refined = 0, 1
parameter, which indicates the boundaries IDs of the wall of the cylinder. The following figure illustrates the mesh:
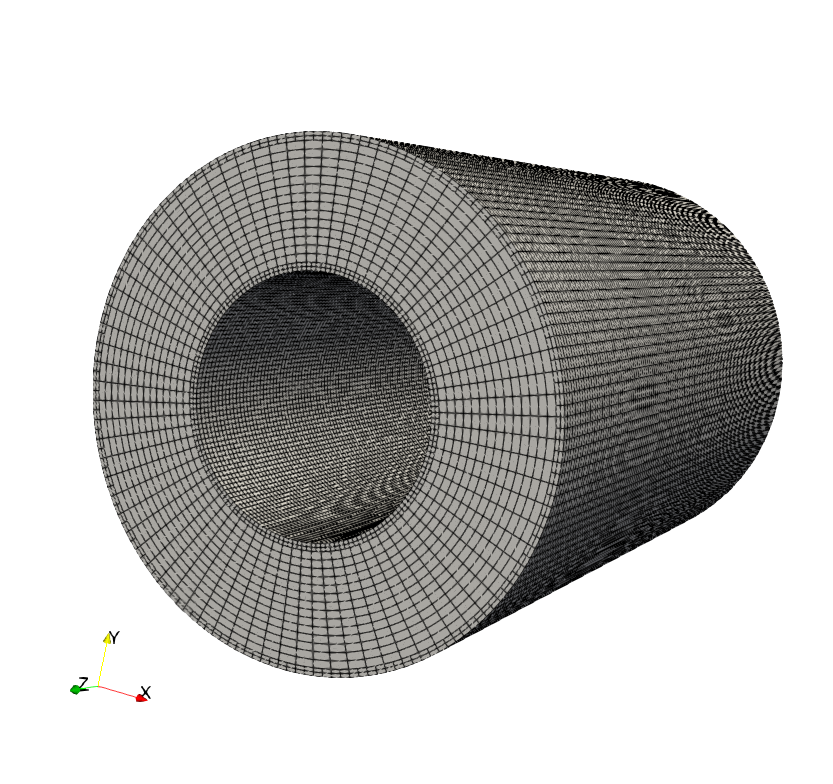
Note
The mesh resolution used in the case study consists of 153,600 cells. If one more initial refinement is used, 942,080 cells are obtained.
Boundary Conditions#
The boundary conditions
subsection establishes the constraints on different parts of the domain:
subsection boundary conditions
set number = 3
subsection bc 0
set type = function
subsection u
set Function expression = -y
end
subsection v
set Function expression = x
end
subsection w
set Function expression = 0
end
end
subsection bc 1
set type = noslip
end
subsection bc 2
set type = periodic
set id = 2
set periodic_id = 3
set periodic_direction = 2
end
end
First, the number
of boundary conditions to be applied must be specified. For each boundary condition, the id
of the boundary (refer to geometry for details of surface id
) as well as its type
must be specified. The inner cylinder (bc 0
) is rotating at a constant angular velocity (\(\omega=1 \ \text{rad/s}\)). We use the type = function
and prescribe a function for the components of the velocity. By prescribing \(\mathbf{u}=[-y,x,0]^T\), we prescribe the rotation of the inner cylinder at an angular velocity of \(1 \ \text{rad/s}\) in the trigonometric direction. The outer cylinder (bc1
) is static and, consequently, a noslip
boundary condition is applied. Finally, a periodic condition is used for the inlet and outlet (bc 2
). The z-
(id=2
) is periodic with z+
(id=3
). For this condition, the periodic direction must be specified. In Lethe, the periodic direction of 2
implies that the normal direction is the \(\mathbf{e}_z\) vector.
Physical Properties#
In the present case, the Reynolds number is defined as: \(Re = \frac{Ud}{\nu}\). Since we set the values of \(U\) and \(d\), the Reynold number of 4000 can be set solely using the kinematic viscosity:
subsection physical properties
set number of fluids = 1
subsection fluid 0
set kinematic viscosity = 6.25e-5
end
end
Initial Conditions#
The initial conditions
subsection lets us set-up the velocity and pressure of the flow at \(t = 0 \ \text{s}\):
subsection initial conditions
set type = nodal
subsection uvwp
# A= -(kappa * kappa) / (1. - kappa * kappa);
# B= ri * ri / (1. - kappa * kappa);
set Function constants = epsilon=0.1, ri=0.5, omega=1.0, d=0.5 , A= -0.3333333333333333, B= 0.3333333333333333
set Function expression = cos(atan2(y,x))*(epsilon*omega*ri*cos(atan2(y,x))*sin(((sqrt(x*x+y*y)-ri)*pi)/ri)*sin(z/d)) - sin(atan2(y,x))*(A*(sqrt(x*x+y*y)) + B/(sqrt(x*x+y*y)) + epsilon*omega*ri*sin(atan2(y,x))*sin(((sqrt(x*x+y*y)-ri)*pi)/ri)*sin(z/d)); sin(atan2(y,x))*(epsilon*omega*ri*cos(atan2(y,x))*sin(((sqrt(x*x+y*y)-ri)*pi)/ri)*sin(z/d)) + cos(atan2(y,x))*(A*(sqrt(x*x+y*y)) + B/(sqrt(x*x+y*y)) + epsilon*omega*ri*sin(atan2(y,x))*sin(((sqrt(x*x+y*y)-ri)*pi)/ri)*sin(z/d)); 0.0; ((0.5*A*A*(x*x+y*y)) + (2*A*B*ln(sqrt(x*x+y*y)))) - (0.5*B*B/(x*x+y*y)) + (0.5*(epsilon*omega*ri)*(epsilon*omega*ri)*cos(2*atan2(y,x))*sin((2*(sqrt(x*x+y*y)-ri)*pi)/ri)*sin(2*z/d))
end
end
The type
is set to nodal
. Then we choose the uvwp subsection
which allows us to respectively set the \(u_x;u_y;u_z;p\) expressions under the function expression
. Switching from cylindrical to Cartesian coordinates results in a quite complex expression. To help with that matter, we use the Function constant
.
FEM Interpolation#
The results obtained for the turbulent Taylor-Couette flow are highly dependent on the numerical dissipation that occurs within the CFD scheme. Generally, high-order methods outperform traditional second-order accurate methods for this type of flow. In the present case, we will compare the usage of second (Q2) and third degree (Q3) polynomial.
subsection FEM
set velocity order = 2 #3 for Q3
set pressure order = 2 #3 for Q3
end
Forces#
The forces
subsection controls the postprocessing of the torque and the forces acting on the boundaries of the domain:
subsection forces
set calculate torque = true
end
By setting calculate torque = true
, the calculation of the torque resulting from the fluid dynamics physics on every boundary of the domain is automatically calculated. Setting verbosity = quiet
will disable the print out on the terminal for each time step.
Post-processing#
subsection post-processing
set calculate kinetic energy = true
set calculate enstrophy = true
end
To monitor the kinetic energy and the enstrophy, we set calculation to true
in the post-processing section.
Simulation Control#
The simulation control
subsection controls the flow of the simulation. To maximize the temporal accuracy of the simulation, we use a second-order bdf2
scheme. Results are written every 10 time-steps. To ensure a more adequate visualization of the high-order elements, we set subdivision = 2
. This will allow Paraview to render the high-order solutions with more fidelity.
subsection simulation control
set method = bdf2
set time step = 0.01
set adapt = true
set max cfl = 1
set time end = 60
set output frequency = 10
set subdivision = 2
end
Tip
A good practice is to use as many subdivisions as the interpolation order scheme.
Other Subsections#
The non-linear solver
and linear solver
subsections use the same parameters as the Taylor-Green Vortex example. More details can be found in this example and a complete overview of the lethe-fluid-matrix-free
linear solver can be found in the the Linear Solver section.
Running the Simulation#
Launching the simulation is as simple as specifying the executable name and the parameter file. Assuming that the lethe-fluid-matrix-free
executable are within your path, the matrix-free simulation can be launched by typing:
and choosing the number of processes n_proc
according to the resources you have available.
Results and Discussion#
The flow patterns generated by the Taylor-Couette flow are quite complex. The following animation displays the evolution of velocity magnitude on the radial-vertical plane (left) and the Q-criterion iso-contours (right), illustrating the vortical structure as the vortex breaks down and generates smaller structures.
Using the enstrophy.dat
file generated by Lethe, the history of enstrophy can be monitored and compared to the reference values extracted from the case study. A plot comparing our simulation results to the reference enstrophy data will be generated by using the following command:
The enstrophy plot features a zoomed section of the enstrophy cascade. The following plot shows the history of the enstrophy as measured with the Q2 scheme:
We note that the enstrophy history does not match either reference scheme. Increasing the order from Q2 to Q3 leads to the following results, which are quite close to the P4 and P5 solutions:
We then revert the scheme order back to Q2 and refine the mesh by setting the initial refinement = 5
in the mesh subsection resulting in a total of 942,080 cells. This simulation closely matches the references for the first 30 seconds and captures the second peak of enstrophy better than the previous simulations:
Finally, employing the finer mesh with Q3 elements actually yields a more accurate prediction of the second peak and certain values of the enstrophy between 30 and 60 seconds.
Considering one more refinement could be interesting to observe if the solution begins to be mesh-independent.
Possibilities for Extension#
This case offers numerous options for postprocessing. Consider exploring alternative quantities such as vorticity and pressure and use the results to generate interesting animations. Feel free to share them with us!
It could also be interesting to explore this case with an even higher Reynolds number