Granuheap#
This example simulates the flow of a cohesive granular material inside a Granuheap instrument using the discrete element method (DEM) solver of Lethe. For more detailed information on the concepts and physical meaning of the parameters, we strongly recommend visiting DEM parameters.
Features#
Solvers:
lethe-particles
Three-dimensional problem
Moving solid surface
GMSH grids
Multi-case simulations
Files Used in This Example#
All files mentioned below are located in the example’s folder (examples/dem/3d-granuheap
).
Mesh file:
cylinder.msh
andsupport.msh
Python file to generate mesh files:
generate_meshes.py
Parameters files for the problem:
granuheap.prm
andgranuheap_multicase.prm
Post-processing python files:
post_processing.py
,post_processing_multicase.prm
andpost_processing_functions.py
.
Description of the Case#
This example simulates the flow of wet sand during a Granuheap experiment. First, particle are inserted inside the cylinder. After \(1.6 \ s\), the cylinder rises, and the particles can flow freely, producing a heap. We compare the numerical results with our experimental results. To remain consistent with the Granuheap experiment, we use the same geometry in our simulations: a cylinder of 0.01m in diameter. For more information about the Granuheap procedures, visit the Granuheap web page. Multiple simulations using different combinations of surface properties are ran to match experiments and simulations. We use the work of Hu et al. [1] as a basis to choose which contact properties will create those combinations.
Generate Mesh Files#
To generate the cylinder.msh
and support.msh
files, we used the generate_meshes.py
file. The two functions take as input the bottom’s position (x0), the radius, the number of points in the circumference, and the height.
cylinder(x0, radius, n_points, height)
support(x0, radius, n_points, height)
In this case, the cylinder has a height of \(2 \ cm\) and a radius of \(0.5 \ cm\). The support has a height of \(0.5 \ cm\) and has the same radius as the cylinder. We fix the number of points in the circumference at 50 for both the cylinder and the support.
cylinder(-0.005, 0.005, 50, 0.02)
support(-0.01 ,0.005 ,50, 0.005)
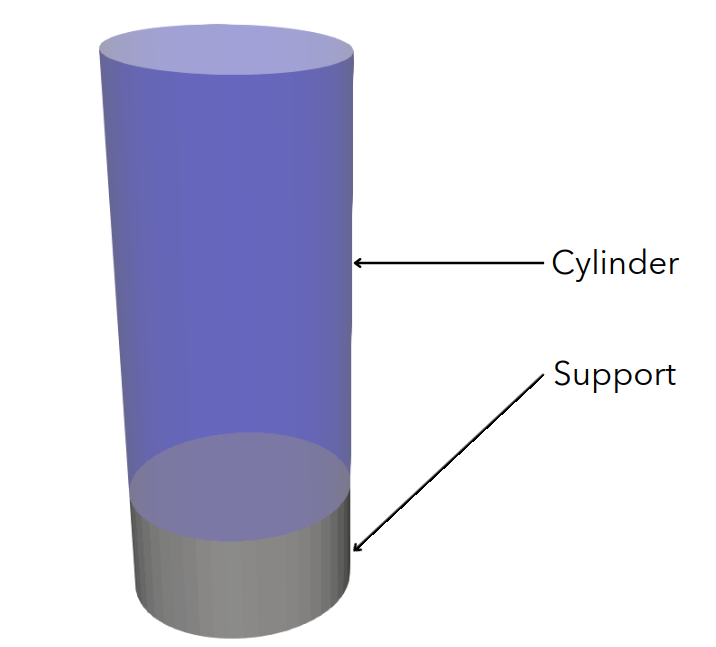
Mesh files can be generated using the following command.
Note
GMSH is needed to generate mesh files. See GMSH website for installation and Introduction on How to Use GMSH for more information.
Parameter File#
Mesh#
The simulation domain is a rectangular box of \(0.045\times0.02\times0.02 \ m\), made using the deal.ii grid generator. The grid is refined 6 times using the initial refinement
parameter so that the cell size is approximately \(1.5\) times the largest particle diameter value in every direction.
subsection mesh
set type = dealii
set grid type = subdivided_hyper_rectangle
set grid arguments = 3,1,1 : -0.010,-0.01,-0.01 : 0.035, 0.01,0.01 : true
set initial refinement = 6
end
Boundaries Conditions#
The bottom of the domain is set as an outlet to allow the particles to leave the domain when they are no longer on the support, thus reducing the computational time of the simulation.
subsection DEM boundary conditions
set number of boundary conditions = 1
subsection boundary condition 0
set boundary id = 0
set type = outlet
end
end
Lagrangian Physical Properties#
The particles have a polydisperse size distribution with a density of \(1922 \ kg/m^3\). \(4\times10^{5}\) particles would be needed to approximately match the \(2 \ g\) of sand used in the experiment. However, to reduce the simulation’s duration of this example, we insert only \(2\times10^{5}\) particles.
According to Hu et al. [1], the angle of repose (AOR) is most influenced by the rolling friction and surface energy parameters. Thus, we simulate twelve combinations of those parameters. The rolling friction
is between \(0.3\) and \(0.7\), and the surface energy
is between \(10^{-3}\) and \(10^{-2}\). The granuheap.prm
file of this example is specifically for a rolling friction
of \(0.5\) and a surface energy
of \(10^{-2}\).
The water volume fraction of the wet sand used in the experiment is \(0.325\%\). According to the work of Liefferink et al. [2], this water volume fraction matches an friction coefficient
of \(0.5\). We use this value as a rough estimate of the friction coefficient
for this example.
subsection lagrangian physical properties
set g = -9.81, 0, 0
set number of particle types = 1
subsection particle type 0
set size distribution type = custom
set custom diameters = 1.02e-4 , 1.16e-4 , 1.33e-4 , 1.52e-4 , 1.75e-4 , 2.00e-4 , 2.29e-4 , 2.62e-4 , 3.01e-4 , 3.44e-4
set custom volume fractions = 0.04 , 0.06 , 0.07 , 0.10 , 0.13 , 0.15 , 0.16 , 0.14 , 0.10 , 0.05
set number of particles = 200000
set density particles = 1922
set young modulus particles = 5.94e4
set poisson ratio particles = 0.4
set restitution coefficient particles = 0.9
set friction coefficient particles = 0.5
set rolling friction particles = 0.5
set surface energy particles = 0.01
end
set young modulus wall = 1e7
set poisson ratio wall = 0.33
set restitution coefficient wall = 0.9
set friction coefficient wall = 0.5
set rolling friction wall = 0.5
set surface energy wall = 1e-4
end
Model Parameters#
The JKR contact model is used in this case because it has be shown to correctly model particle agglomeration for wet sand [1] .
subsection model parameters
subsection contact detection
set contact detection method = dynamic
set dynamic contact search size coefficient = 0.9
set neighborhood threshold = 1.3
end
subsection load balancing
set load balance method = frequent
set frequency = 10000
end
set particle particle contact force method = hertz_JKR
set rolling resistance torque method = constant_resistance
set particle wall contact force method = JKR
set integration method = velocity_verlet
end
subsection restart
set checkpoint = true
set frequency = 10000
set restart = false
set filename = dem
end
end
Particle Insertion#
An insertion box is defined inside the cylinder.:math:10^{4} particles are inserted every \(9000\) iterations. The size of the insertion box is chosen to ensure it is completely inside our cylinder which is smaller than our domain. Otherwise, particles will be lost during the insertion stage.
subsection insertion info
set insertion method = volume
set inserted number of particles at each time step = 10000
set insertion frequency = 9000
set insertion box points coordinates = 0.015, -0.00325, -0.00325: 0.035, 0.00325, 0.00325
set insertion distance threshold = 1.2
set insertion maximum offset = 0.05
set insertion prn seed = 19
set insertion direction sequence = 1, 2, 0
end
Solid Object#
We set the cylinder’s translational velocity to \(0.05 m/s\) after the particles were loaded, thus when the simulation time is larger than \(1,6 \ s\).
subsection solid objects
subsection solid surfaces
set number of solids = 2
subsection solid object 0
subsection mesh
set type = gmsh
set file name = cylinder.msh
set simplex = true
end
subsection translational velocity
set Function expression = if (t>1.6, 0.05, 0) ; 0 ; 0
end
end
subsection solid object 1
subsection mesh
set type = gmsh
set file name = support.msh
set simplex = true
end
end
end
end
Simulation Control#
The process duration lasts for \(2.2 \ s\). We output the simulation results in every \(1000\) iterations.
subsection simulation control
set time step = 7.54e-6
set time end = 2.2
set log frequency = 1000
set output frequency = 1000
set output path = ./output/
set output name = granuheap
set output boundaries = true
end
Running the Simulation#
Running one case#
A simulation with one set of values for the rolling friction
and the surface energy
can be launched using the following command:
Note
This example needs a simulation time of approximately 5 hours on 12 processors using an AMD Ryzen 9 5900x 12-core processor.
Running multiple cases#
Three files are needed to create and launch multiple simulations; generate_cases_locally.py
, granuheap_multicase.prm
and launch_lethe_locally.py
. For more information, visit How to Automatically Create and Launch Lethe Simulations
In this case, we run 3 different values of rolling friction
and 4 different values of surface energy
, for a total of 12 simulations.
number_of_cases = 4
# Generation of data points
energy_first = 0.0010
energy_last = 0.0100
energy = np.linspace(energy_first, energy_last, number_of_cases)
rolling_friction_first = 0.3
rolling_friction_last = 0.7
rolling_friction = np.linspace(rolling_friction_first, rolling_friction_last, number_of_cases-1)
Simulations can be launched using the following commands:
Post-processing#
The Granuheap device captures 16 pictures around the heap in a 180-degree arc. The images generate a map that distinguishes areas with constant particle presence (black), no particle presence (white), and varying particle presence (expressed through different shades of gray). The image below shows the map of the wet sand experiment and is provided as experimental_result.png
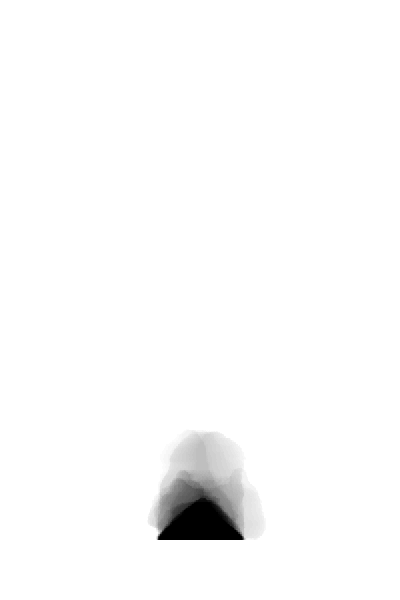
Running one case#
To compare only one simulation with the experimental results, the post_processing.py
file can be launched using the following command.
The post-processing feature is launched using PvPython, the Python interface to the Paraview Software. It allows users to control ParaView with Python, thus without opening the user interface. PvPython can also run python scripts.
If the experimental file is not the one provided in this example, the exp_path
, height_exp
, and width_exp
will need to be updated in the post_processing.py
file.
# Path to the granuheap experimental result
exp_path = 'experimental_result.png'
# Name of simulation output (see OUTPUT NAME set in the simulation subsection of the parameter file)
num_output = 'granuheap'
# Output path (see OUTPUT PATH set in the simulation subsection of the parameter file)
out_path = 'output'
# Number of pixels in height and width of your experimental support (to adjust if you change experimental result)
height_exp = 60
width_exp = 85
This file will generate a map of the simulation and subtract it from the experimental map to obtain the profile shape error. This error will be presented in a new image saved as image_difference.png
. The picture below presents the profile shape error for a rolling friction
of 0.5 and a surface energy
of 0.0100.
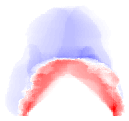
This post_processing file will also output the Root Mean Square Error (RMSE) in the terminal.
Running multiple cases#
For multiple cases, the post_processing_multicase.py
file should be used using the following command.
If the experimental file is not the one provided in this example, the exp_path
, height_exp
and width_exp
will need to be updated in the post_processing_multicase.py
file. The parameters’ names and values for each case can also be modified in the python file.
# Path of the granuheap experimental result
exp_path = 'experimental_result.png'
# Name of directory for each simulation (see CASE_PREFIX from the launch_lethe_locally.py file used)
num_name = 'wetsand'
# Name of simulation output (see OUTPUT NAME set in the simulation subsection of the parameter file)
num_output = 'granuheap'
# Output path (see OUTPUT PATH set in the simulation subsection of the parameter file)
out_path = 'output'
# Definition of variable parameters
parameter1_name = 'Surface Energy'
parameter1 = [0.0010, 0.0040, 0.0070, 0.0100]
parameter2_name = 'Rolling Friction'
parameter2 = [0.70, 0.50, 0.30]
# Number of pixels in height and width of your experimental support (to adjust if you change experimental result)
height_exp = 60
width_exp = 85
The code will generate a map for each simulation and then subtract them from the experimental map. Those errors will be presented in a new image saved as profile_shape_error.png
.
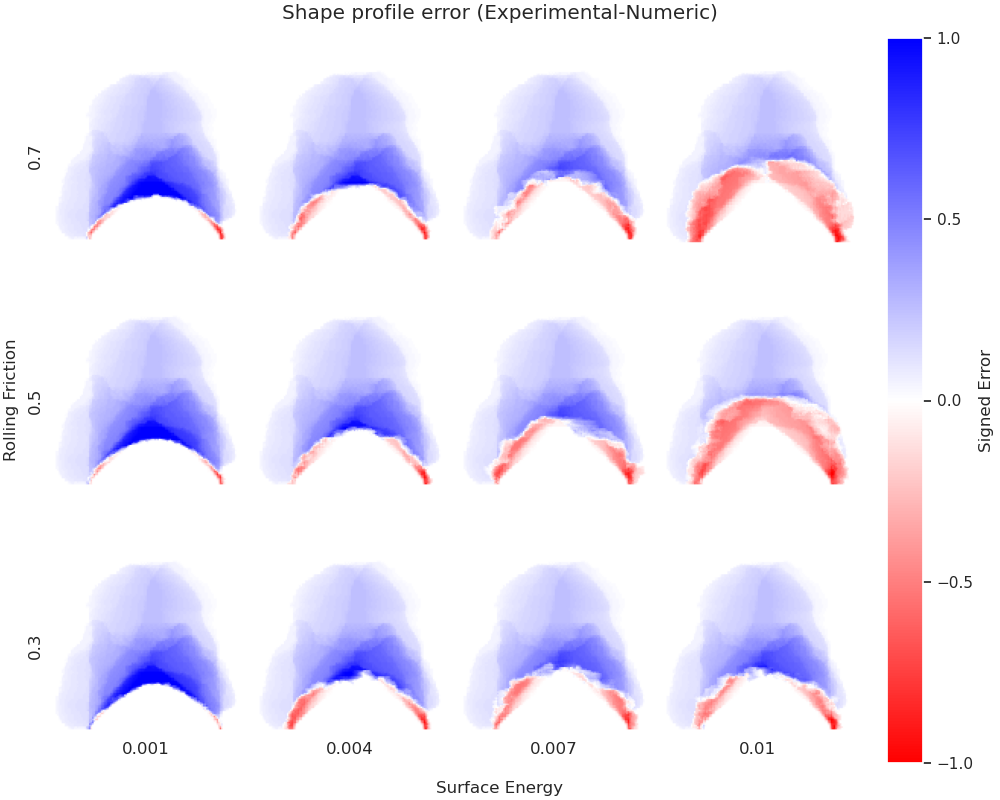
To confirm which simulation has the lowest error, an image saved as error_values_heatmap.png
will present a heatmap of each simulation RMSE.
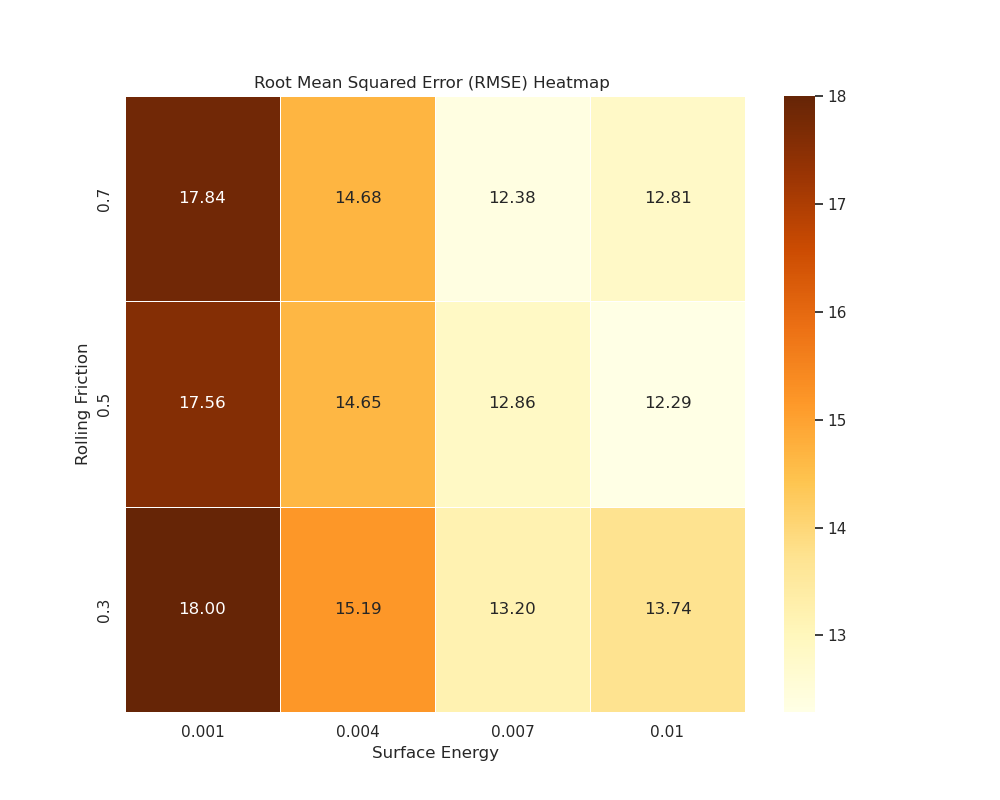
The lowest error is obtained when the rolling friction
is 0.5 and the surface energy
is 0.0100.
Note
The following libraries will be necessary to run post-processing files; PIL, numpy, matplotlib.pyplot, os, glob, scipy.interpolate and UnivariateSpline. The Paraview software is also needed.
Results#
The video below presents the Granuheap simulation for a rolling friction
of 0.5 and a surface energy
of 0.0100.